How Filler Masterbatch Reduces Material Costs Without Compromising Quality
Date: 18th December 2024 14:46 PM
In today’s competitive plastic manufacturing landscape, reducing material costs while maintaining high-quality standards is a constant challenge. This is where Filler Masterbatch emerges as a game-changer. By offering a cost-effective solution to replace a portion of virgin polymer without sacrificing performance, Filler Masterbatch Manufacturers are helping industries across the globe achieve greater efficiency and sustainability.
The Role of Filler Masterbatch in Plastic Manufacturing
Filler Masterbatch is a compound made by combining high-quality fillers like calcium carbonate with a polymer carrier resin. This blend not only reduces raw material expenses but also enhances specific mechanical and aesthetic properties of the final product. For instance, leading Masterbatch Manufacturers incorporate advanced techniques to ensure that the masterbatch blends seamlessly with polymers, making it suitable for diverse applications such as packaging, extrusion, and injection molding.
India is emerging as a hub for Filler Masterbatch Manufacturers in India, known for their innovative and eco-friendly formulations. Companies in this region are investing in advanced technologies to produce cost-effective solutions that meet global quality standards, further solidifying their reputation in the global market.
How Filler Masterbatch Reduces Material Costs
- Replacement of Virgin Polymer: One of the primary advantages of Filler Masterbatch is its ability to replace expensive virgin polymers like polyethylene and polypropylene. This substitution not only cuts down costs but also helps in optimizing raw material consumption without compromising the product’s integrity.
- Bulk Density Optimization: By improving the bulk density of the material, Calcium Carbonate Filler Masterbatch reduces the overall material requirements per product, leading to significant cost savings in production.
- Reduced Energy Consumption: High-quality Filler Masterbatch Manufacturers ensure that their products enhance the processability of plastics. This translates to lower energy requirements during processing, further cutting operational costs.
- Waste Minimization: Advanced Masterbatch formulations reduce material wastage during production. This makes them a sustainable choice for manufacturers looking to minimize their environmental footprint while saving costs.
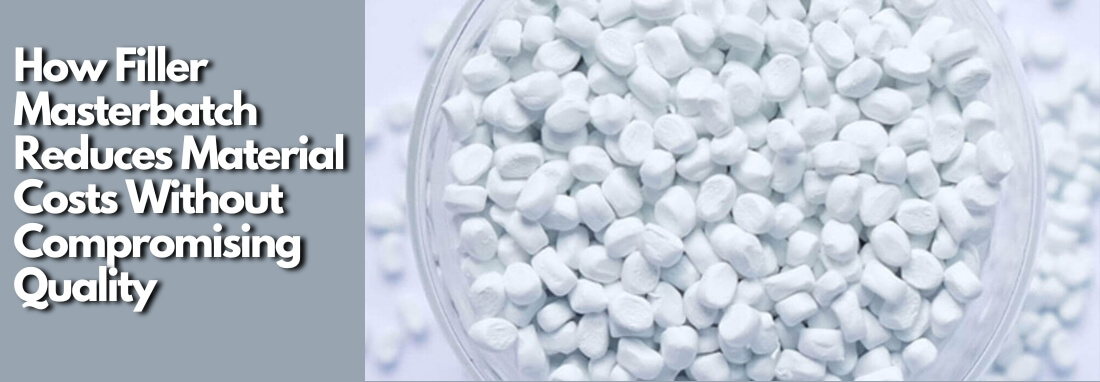
Enhancing Quality Without Compromise
While cost reduction is a significant benefit, Filler Masterbatch does not compromise on quality. Instead, it offers several advantages that improve the performance and aesthetics of the final product:
- Improved Mechanical Properties: The addition of fillers like calcium carbonate enhances the strength, rigidity, and durability of the product. This makes Filler Masterbatch ideal for applications in construction, automotive, and packaging industries.
- Better Aesthetic Appeal: Products made with Filler Masterbatch exhibit improved surface finish and uniformity, ensuring a premium look and feel. Filler Masterbatch Manufacturers prioritize consistent particle distribution to achieve this.
- Eco-Friendly Solutions: Many manufacturers offer Eco-Friendly Filler Masterbatch Options, contributing to sustainability goals without compromising on product quality.
- Customization for Specific Applications: Leading Filler Masterbatch Manufacturers in India provide tailor-made solutions to meet specific industry requirements, ensuring that quality standards are met or exceeded.
Applications of Filler Masterbatch
- Plastic Manufacturing: Widely used in the production of films, sheets, and injection-molded products, Filler Masterbatch is a staple in the plastic industry. It helps in reducing costs while maintaining the structural integrity of the product.
- Extrusion Processes: High-performance Filler Masterbatch enhances the extrusion process by improving material flow and reducing defects.
- Blown Film Applications: The use of Filler Masterbatch in blown film applications ensures better thickness control and improved tear resistance.
- Injection Molding: In injection molding, Filler Masterbatch optimizes resin consumption and enhances the dimensional stability of the final product.
- Packaging Industry: The packaging industry benefits from Cost-Effective Filler Masterbatch Solutions by producing lightweight yet durable materials for bags, containers, and wraps.
Why Choose Filler Masterbatch from India?
India has become a leading supplier of High-Quality Filler Masterbatch due to its advanced manufacturing capabilities and cost-effective production. Here are some reasons to choose Filler Masterbatch Manufacturers in India:
- Innovative Technology: Indian manufacturers leverage advanced technology to produce Sustainable Solutions with Filler Masterbatch.
- Global Standards: Products from Masterbatch Manufacturers in India meet international quality benchmarks, making them a preferred choice for global buyers.
- Custom Solutions: Indian companies specialize in offering tailored solutions to suit diverse industrial needs, from packaging to construction.
Conclusion
Filler Masterbatch has revolutionized the plastic industry by providing a cost-effective yet high-quality alternative to virgin polymers. From reducing material costs to enhancing product performance, the benefits of using Filler Masterbatch are undeniable. By sourcing from reputable Filler Masterbatch Manufacturers and Masterbatch Manufacturers, businesses can achieve significant cost savings and improved product quality.
With the growing demand for sustainable and efficient solutions, Filler Masterbatch Manufacturers in India are at the forefront of innovation, offering advanced products that cater to a wide range of applications. As industries continue to prioritize both cost-efficiency and quality, Filler Masterbatch remains a vital component in achieving these goals.